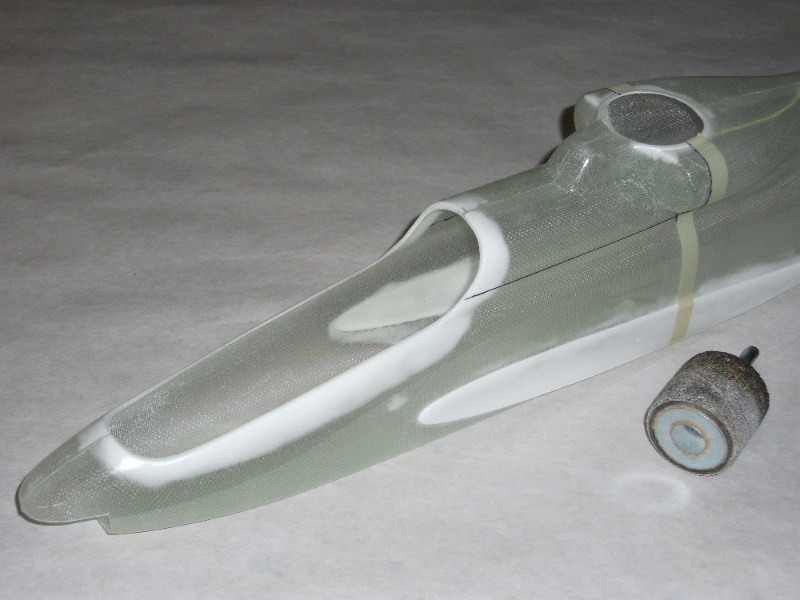
First up, mark and carefully cut out the opening for the main
shaft and swash plate. With the opening completed and
sanded, the access hatch is marked with a Sharpie pen. On my
Cheyenne I opted for the smallest possible hatch, and while this
looks very nice, it does make installing and removing the
mechanics a very tight squeeze. The larger alternative hatch
shown on the plans will make access easier and is required if you
use the stock 150T main gear. The larger hatch can also make
canopy installation easier.
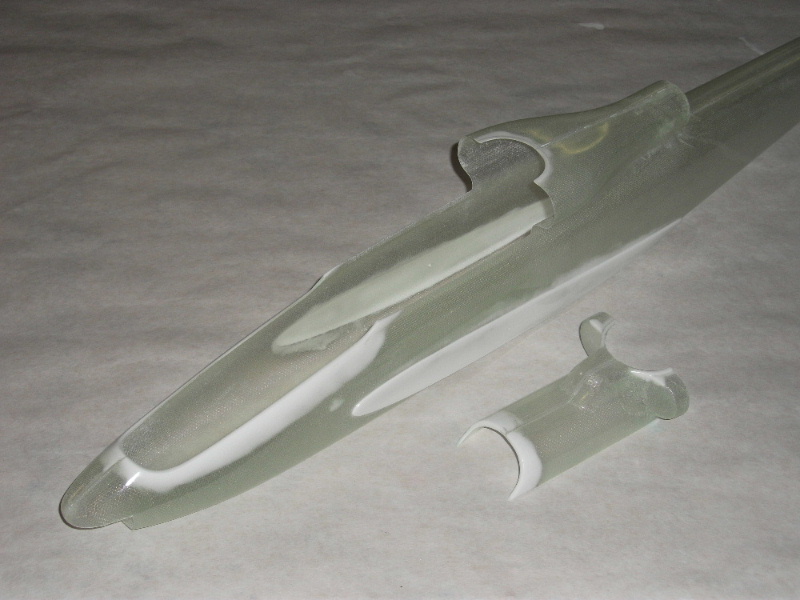
The hatch is very carefully cut free. Use a thin razor saw,
tape a metal straightedge in place as a guide, and
take your time!
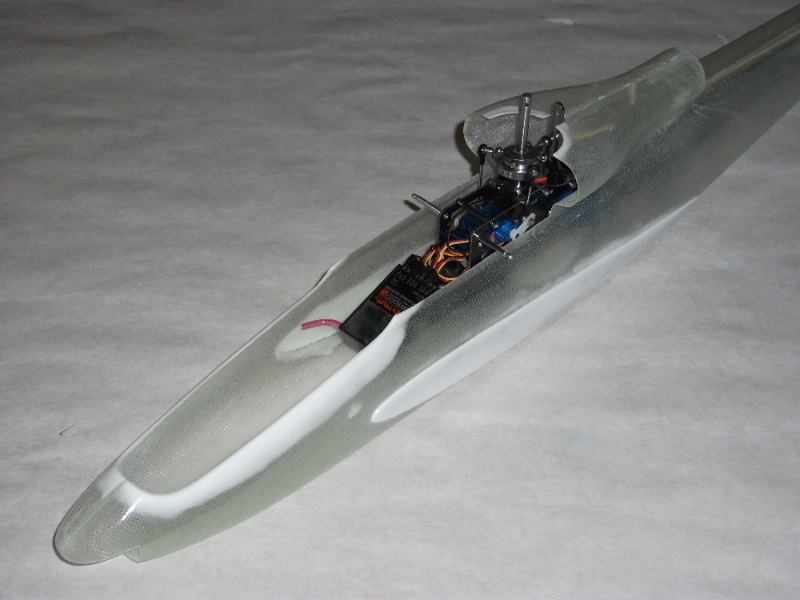
The mechanics slip neatly into place. The sponsons that
house the retracts will stiffen the forward fuselage dramatically.
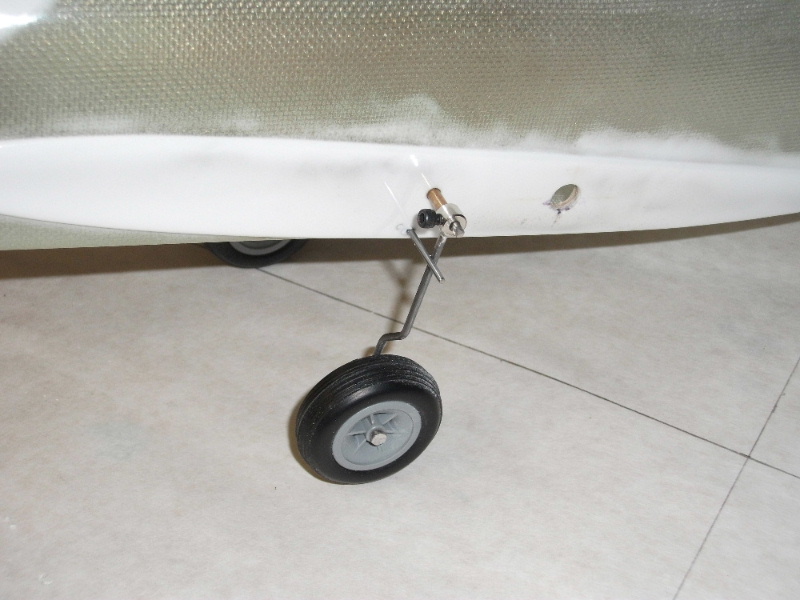
The retractable landing gear simply pivot on an axle which is
supported by the 1/16" ply doublers beneath the 1/8" bearers for
the mechanics.
Make sure the pivot for the landing gear is positioned far enough
back so that it doesn't interfere with the motor.
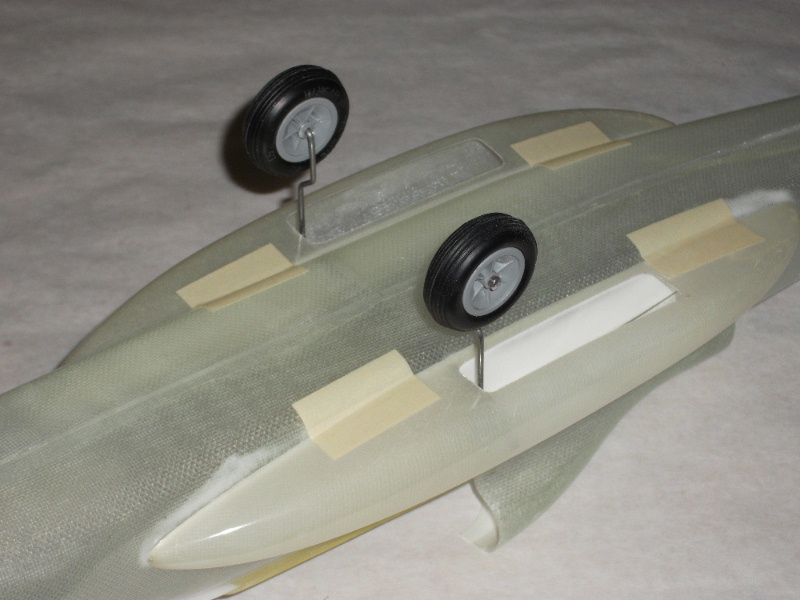
With the retract installation complete the sponsons can be test
installed. Note: The sponsons should not be glued in
place until the wing joiner sockets are installed (see below).
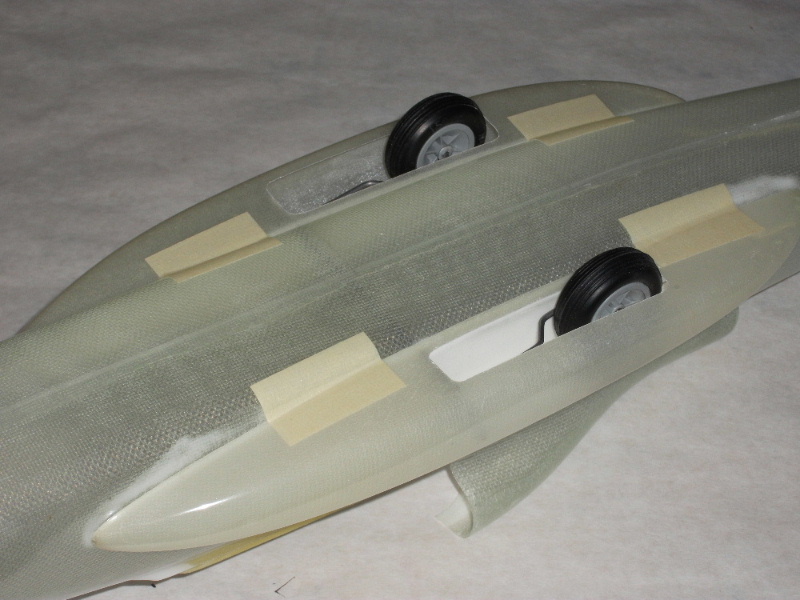
The retracts fold neatly back into the wells. The wheels are
partially exposed just as on the full-scale Cheyenne.
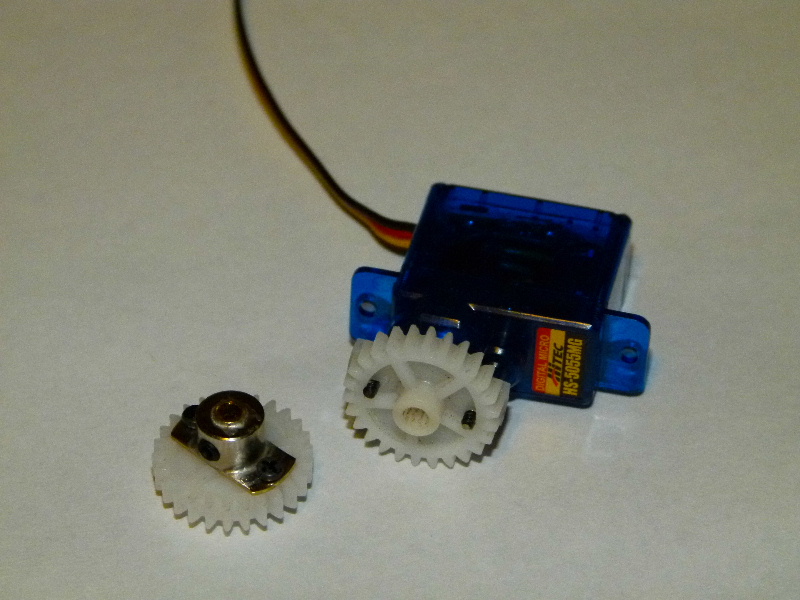
The retracts are actuated by a metal gear micro servo. I
used scrap tail drive gears, as they were light and compact and
strong enough for the application.
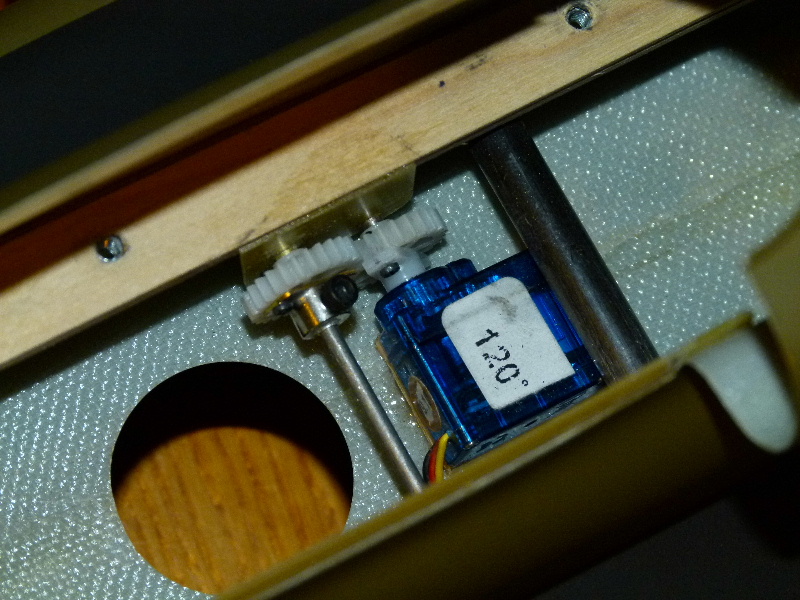
Here's the retract servo installed. Note that the 1/32 G10
plate supports the servo's output shaft. This simple
mechanism has worked perfectly.
In this view you can also see the clearance/cooling hole for the
Scorpion HK-2221-12 motor.
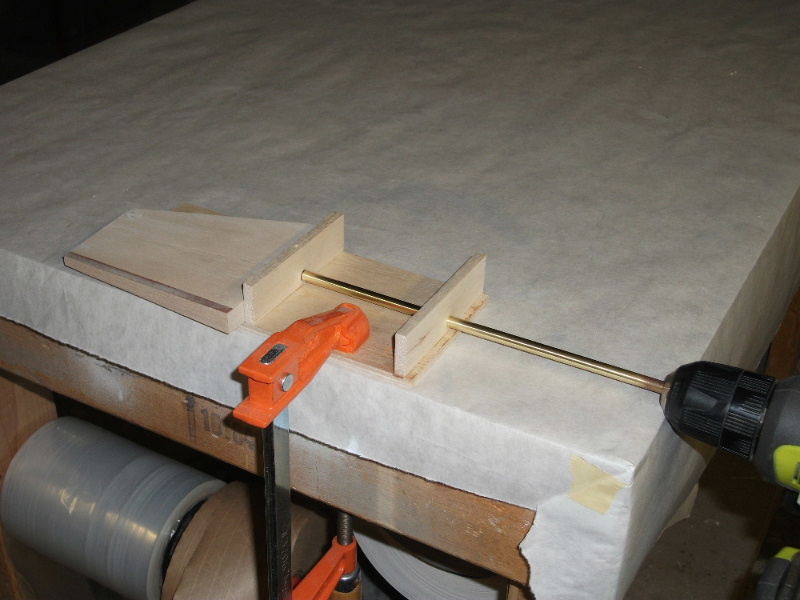
I made this jig to drill the holes for the carbon fiber wing
joiners. In truth, you could also install them by simply
cutting slots in the wings, epoxying the joiners in place and then
filling the slots with scrap balsa. Just be careful to get
the dihedral angle and alignment correct.
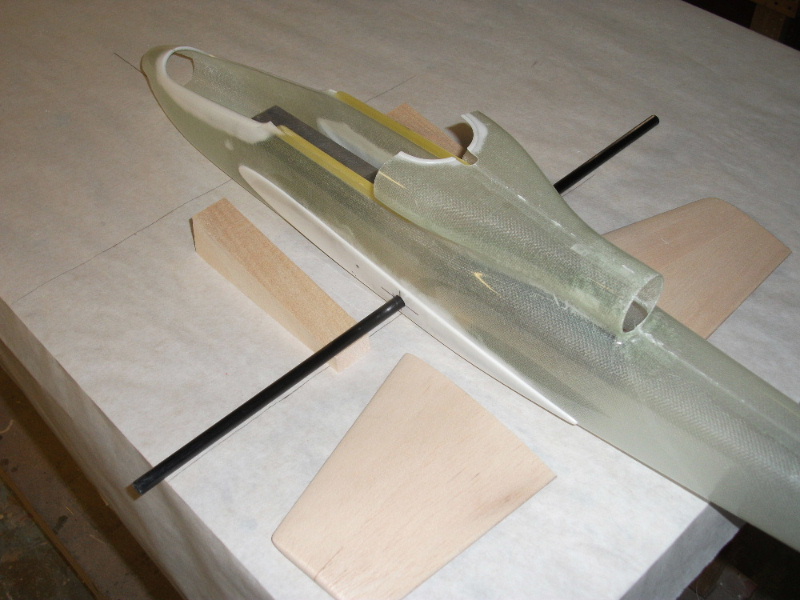
Here the female wing joiner socket is being installed in the
fuselage. Be careful to get the socket absolutely horizontal
and square. I recommend leaving the over-length socket free
to slide back and forth. This will make it easier to cut the
holes in the sponsons in the exact right spot. Once the
sponsons are installed the socket can be trimmed to length and
glued in place.
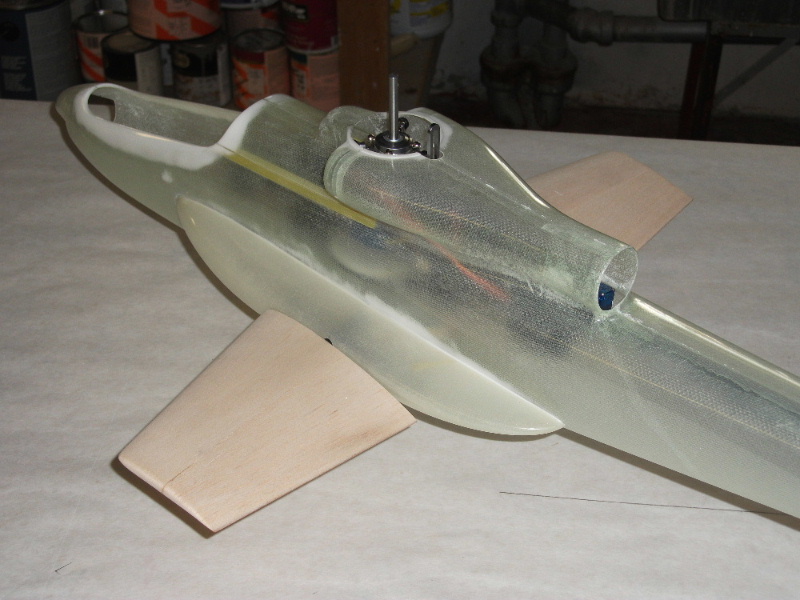
Here the wings are fitted into place. Use 1/16" music wire
for the anti-rotation pins near the leading edges. I also
drilled through the joiners inside the wheel wells and installed
1/32" music wire retainer pins. This locks the wings in
place, but allows quick removal for travel.
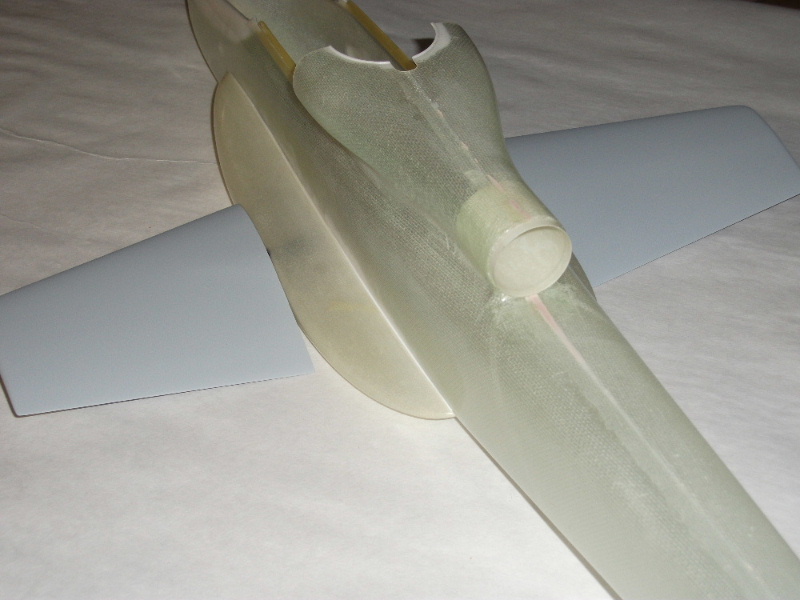
I recommend glassing the wings with 0.56 ounce fiberglass and
finishing epoxy. Then, after applying clear tape to the
sponsons as a release liner, the wing roots are molded with
Bondo. After the Bondo partially cures the wings are popped
free and the Bondo is block sanded flush with the wing
surface. The result is a perfect joint.
Note that the exhaust pipe has been formed from a strip of paper
saturated with finishing resin. The strip is rolled up
tight, slipped into place and then expanded to be a tight
fit. The excess is trimmed flush after the resin
cures.
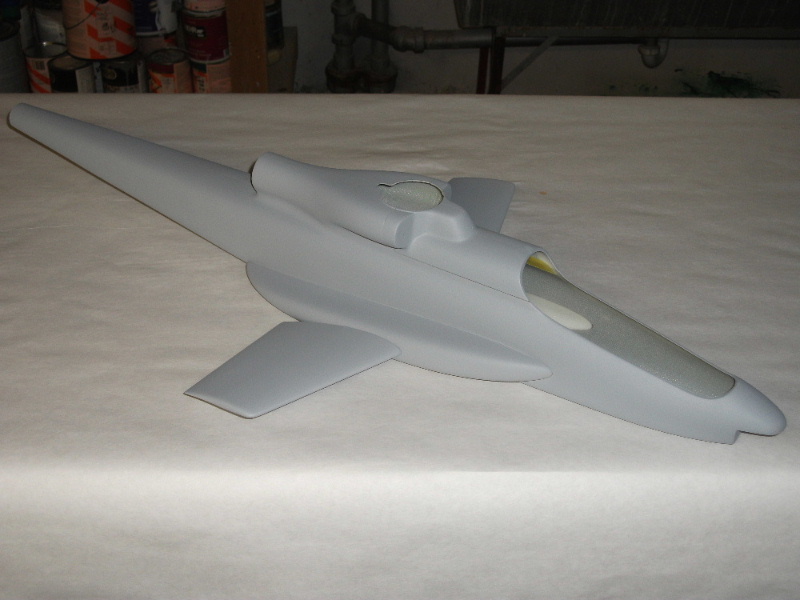
We're nearly there! The fuselage has received a final coat
of primer preparatory to painting.